Bonding WPS for Beginners: Beginning with Welding Treatment Specifications
Grasping Welding WPS Specifications: Best Practices and Techniques for High Quality Welds
In the world of welding, understanding Welding Procedure Requirements (WPS) criteria is an essential part that directly affects the high quality and integrity of welds. As we browse through the details of welding WPS standards, uncovering essential insights and approaches for achieving top-tier welds will be critical for welders looking for to succeed in their craft and produce welds that stand the test of time.
Recognizing Welding WPS Requirements
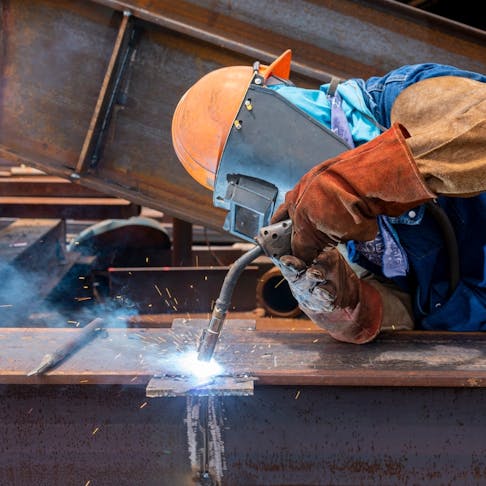
Recognizing WPS criteria is vital for engineers, assessors, and welders involved in welding operations. By adhering to WPS guidelines, welders can generate welds that fulfill the needed mechanical buildings and structural integrity. Assessors depend on WPS paperwork to verify that welding procedures are being followed properly which the resulting welds are of top quality. Designers make use of WPS criteria to make welding treatments that make certain the toughness and integrity of welded structures.


Important Devices for Top Quality Welds
Mastering welding WPS requirements is essential for welders to effectively utilize the crucial tools needed for creating top quality welds. The type of welding maker needed depends on the welding process being made use of, such as MIG, TIG, or stick welding. Wire brushes and breaking hammers are important for cleansing the weld joint prior to and after welding to get rid of any contaminations that can influence the quality of the weld.
Key Strategies for Welding Success
To achieve welding success, one have to master the vital techniques important for creating top quality welds. One critical strategy is maintaining the right arc length. Maintaining the electrode at the optimum range from the workpiece is vital for creating solid, consistent welds. In addition, controlling the travel rate is critical. Moving as well quickly can result in inadequate infiltration, while relocating also gradually can bring about extreme warm input and possible issues. Appropriate adjustment of the electrode angle is one more essential technique. The angle at which the electrode is held can impact the bead shape and infiltration of the weld. Furthermore, guaranteeing regular gun angle and direction of traveling is vital for harmony in the weld grain. Last but not least, maintaining a steady hand and a steady welding position throughout the procedure is key to achieving accuracy and consistency in the welds. By grasping these vital methods, welders can boost the high quality of their work and attain welding success.
Ensuring Compliance With WPS Standards
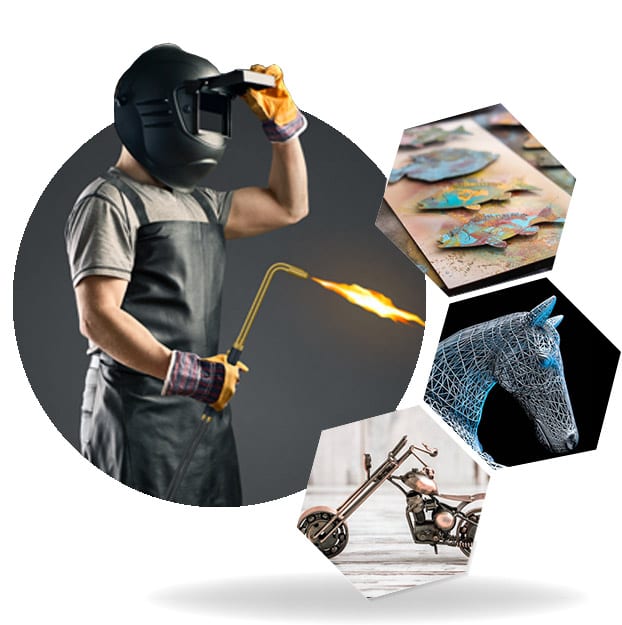
Furthermore, maintaining in-depth documents of welding parameters, equipment calibration, and inspection results is essential for demonstrating compliance with WPS requirements. By diligently sticking to WPS standards, welders can ensure that their job fulfills the necessary top quality levels and contributes to the total success of the welding job.
Troubleshooting Common Welding Issues
To resolve this, making certain proper cleansing of the base metal prior to welding and making use of the correct protecting gas can dramatically reduce porosity. Additionally, distortion, cracking, and spatter are common welding obstacles that can be minimized through proper joint preparation, consistent warmth control, and choosing the proper welding consumables. By completely comprehending these typical welding concerns and their root creates, welders can properly troubleshoot problems and accomplish high-grade welds.
Final Thought
To conclude, mastering welding WPS standards needs a detailed understanding of the standards, making use of important source crucial tools, and implementing vital strategies for successful welds. Ensuring conformity with WPS standards is important for generating quality welds and staying clear of typical welding problems. By following ideal methods and methods, welders can achieve regular and trustworthy results in their welding tasks.
In the world of welding, understanding Welding Procedure Specification (WPS) requirements is an essential component that straight influences the top quality and stability of welds.When diving into the world of welding techniques, a vital element to comprehend is the value and complexities of Welding Treatment Specification (WPS) standards. WPS requirements provide a thorough browse around this site standard for welding operations, ensuring consistency, high quality, and security in the welding process. The type of welding device needed depends on the welding process being made use of, such as MIG, TIG, or stick welding.Achieving welding success through the mastery of crucial techniques requires a comprehensive understanding and adherence to Welding Treatment Spec (WPS) requirements.